
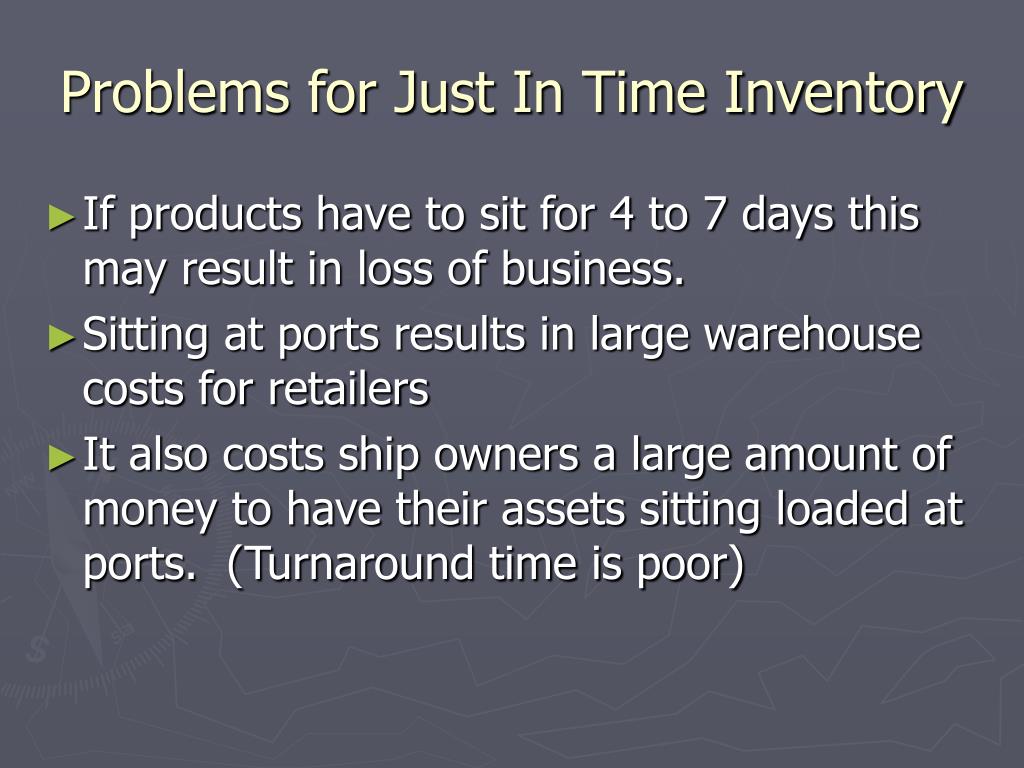
Once it manufactures the clothing, it sits in a warehouse until orders start coming in. Suppose a clothing manufacturer produces items in bulk, assuming retailers will order them. JIT also helps to reduce inventory waste. For example, because Toyota doesn’t order parts until a customer places an order, the company knows it won’t spend money making products it won’t be able to sell. JIT can help companies cut down on waste and costs. In the decades since Toyota created the just-in-time (JIT) system, companies have continued to use it to improve supply chain management. The manufacturer only orders as many raw materials as it needs to produce goods right now, as it doesn’t want supplies sitting unused.
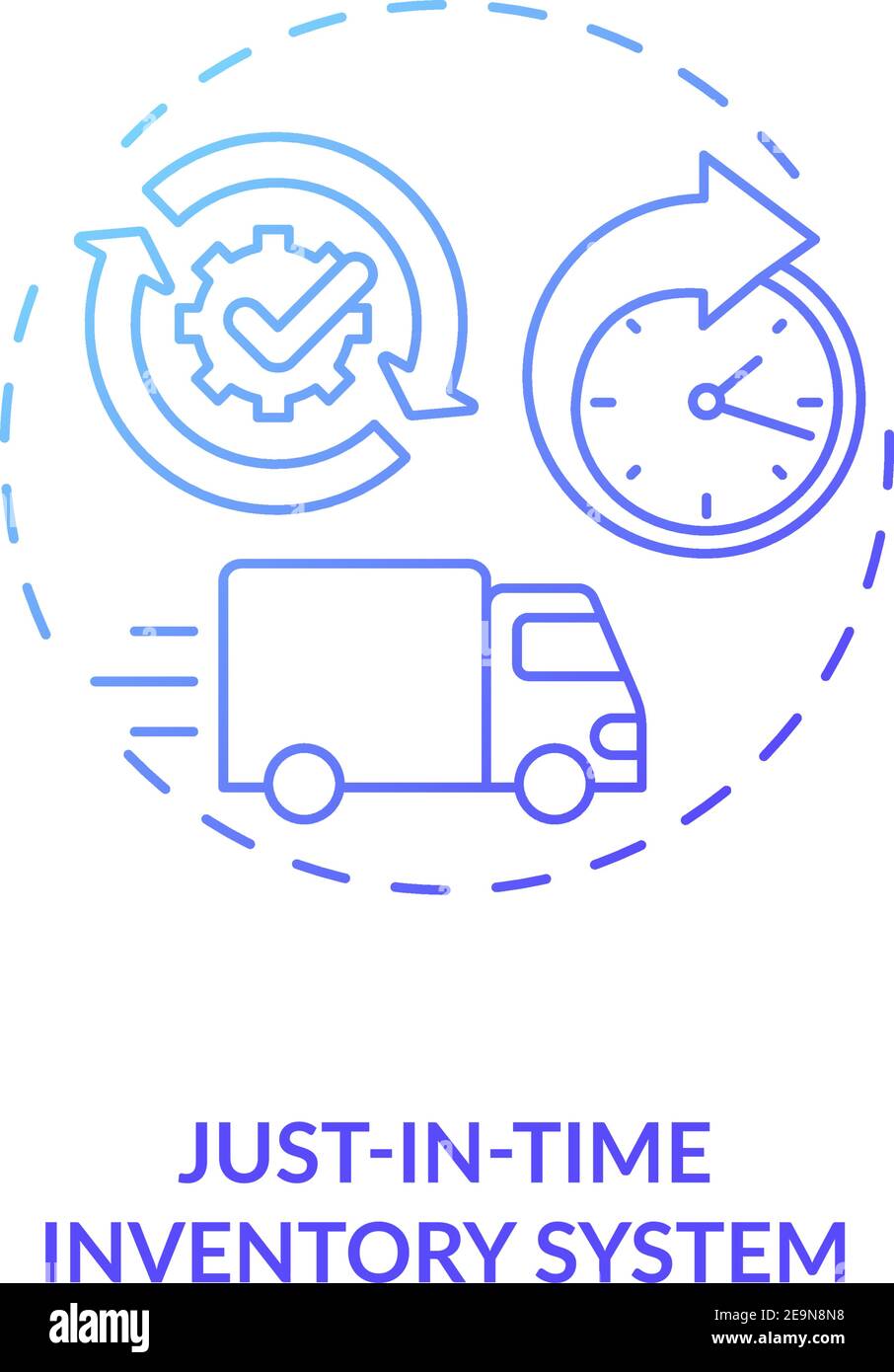
The goal is to avoid unused inventory sitting in a warehouse or storeroom, which can be expensive and result in waste or damaged products. A retailer using a JIT inventory system doesn’t want more finished goods delivered until it’s actually ready to sell them. Finally, the manufacturer notifies its suppliers that it needs the materials to move forward with production. The retailer sends a signal to the manufacturer that it’s time to create and deliver more products. At a certain point, this gives the retailer a cue that it’s time to order more goods.
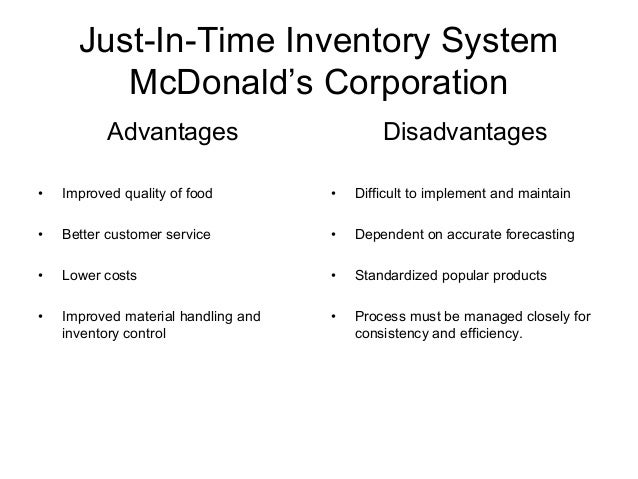
Starting at the end of the supply chain, a consumer signals to the retailer that there’s demand for a product by placing an order or going to a store to buy it. These signals, often a reorder slip or a computerized version of one, exist at each step of the supply chain, from the raw material suppliers to the customers. JIT uses kanbans (which translates to “signal cards”) - visual cues that let companies know when it’s time to move more products. This is an alternative to a “push” approach, where companies manufacture goods in hope that people will buy them. Just-in-time (JIT) is based on a “pull” approach - the manufacturing process is driven by demand from customers. The company then replaces the parts it used in the production process. When the company receives a vehicle order, it collects the necessary parts and begins the production process. Toyota still uses JIT today, making only the goods that are needed. But manufacturers who weren’t using this production model continued to build cars, even though no one was buying them. Because of its lean production model, Toyota was able to quickly pull back on manufacturing. In 1973, many of the world’s oil-producing countries announced they would be cutting supply and increasing prices. The Toyota leaders returned to Japan with what they’d learned and started to implement just-in-time (JIT), producing cars in response to demand. They observed that some auto companies were mass-producing more vehicles than customers were buying, putting a streamlined process ahead of customers’ needs. Around 1950, it sent representatives from Japan to the US to study the production process there. The Toyota Motor Company began making cars in 1935. That way, there’s no chance of anything going to waste. Rather than ordering ahead for the week or the month, the retailer gets a delivery of 25 bottles each day. Suppose a retailer that offers bath products knows it sells 25 bottles of lotion a day. Using this system, a retailer only orders as many products as it will sell right away. JIT also applies to the amount of inventory a store keeps in stock.

There isn’t a large supply of materials on the production floor waiting to be put to use. Once that happens, the company orders the necessary materials and produces vehicles. Instead, the company waits until a dealership places an order. Toyota, for example, doesn’t proactively build a shipment of cars. In JIT manufacturing, a company only orders the materials and supplies it needs to meet current demand. It helps make the supply chain more efficient by ensuring that products and materials only arrive at the exact time and in the exact quantity that’s necessary. Just-in-time (JIT) is a system companies can use to manage inventory ( the raw materials and finished goods a company has on hand).
